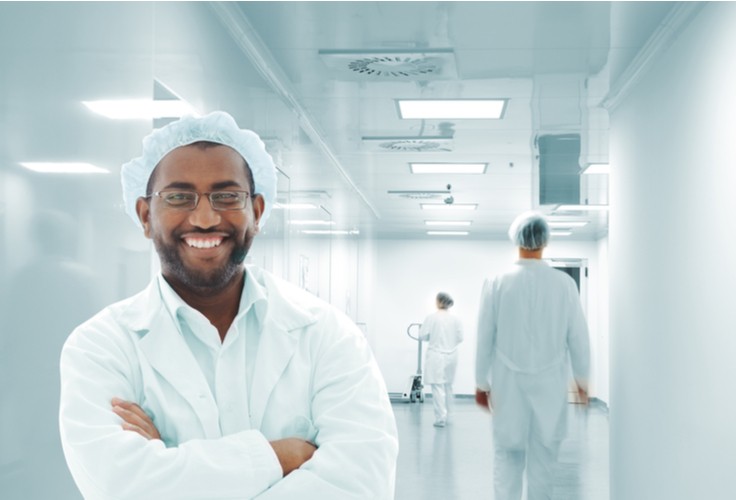
Cleanroom shutdown events occur for numerous reasons, planned and unplanned. In returning to normal operation, there are key best practices that can be followed for a successful return to normal operation.
In cleanroom operations, maintenance is of critical importance to uphold the integrity, safety and proper operation of the cleanroom. However, it can be difficult to carry out maintenance while the cleanroom is in operation. For this reason, cleanrooms are typically fully or partially shut down at least once each year for scheduled maintenance. Cleanrooms may also be shut down for installation of new equipment, equipment repair, or other improvements. The final, most serious reason for cleanroom shutdown is an unplanned event – such as air handling system failure, or extreme weather events.
Whether your cleanroom is shut down for a planned or unplanned event - specific cleanroom procedures should be followed during and after the shutdown.
Cleanroom Procedures Prior to Shutdown/Preventing Shutdowns
Appropriate actions prior to shutdowns will ensure successful transition into and out of shutdown. It is recommended to generate and maintain a cleanroom shutdown Standard Operating Procedure which describes the requirements for actions during shutdown and following shutdown.
- Include items such as what to monitor during shutdown, criteria that must be met for normal operation to proceed, and responsible parties for each action
- Define testing and certification activities required, this may be further classified by the type of shutdown event (planned v unplanned), and reasonable unplanned events that might be expected (for example, typical extreme weather events in the region)
- Common monitored items include temperature, humidity and non-viable particulate levels
- Define required cleaning by area, surface, and shutdown type. Include any required sampling following cleaning.
While there are several actions to take to ensure a successful shutdown and return to normal operation, the best solution is to implement safeguards to prevent unplanned shutdowns.
These safeguards may include uninterrupted power supplies (UPSs) or generators to prevent loss of power, or other backup systems to maintain standard operating in the event of a system failure.
Cleanroom Procedures During Shutdown
- If work is occurring at the time of an unplanned shutdown, stop work , secure any finished product, note time and status of process, attempt to seal any remaining ingredients to be filled to avoid exposure to uncontrolled air, initiate tear down of process.
- Ensure that the time of shutdown is documented, including on any processes currently in progress.
- Monitor and document temperature, humidity and particle levels at regular intervals throughout the shutdown., or as required by your shutdown SOP.
- Complete required testing and certification, sampling, and cleaning as described by the shutdown SOP. This may include HEPA filter testing, airflow measurement and room air exchange rate calculation, differential pressure measurement, particle counting, and viable sampling depending on the nature and duration of the shutdown.
Review testing results to confirm cleanroom operation status has returned to required normal limits.
Cleanroom Procedures Following Shutdown
Following shutdown, it is important to review the cause for shutdown if the event was unplanned. Assessment of the cause will allow for potential prevention of recurrence. Additional actions might include:
- Revision of SOP to include lessons learned from shutdown
- Retention of documentation from shutdown monitoring and post-shutdown testing, certification, cleaning, and sampling
- Continued monitoring for a pre-defined interval, depending on the nature of shutdown and conditions of cleanroom release to normal operation
The cleanroom procedures described here for planned and unplanned shutdowns is not an exhaustive summary. Review of the critical aspects related to each facility and process should be considered in shutdown plan development and implementation, and risk assessment practices should be used.
Technical Safety Services provides cleanroom services that can help you resume work following any shutdown — major or minor. For more information and to discuss your plans or needs, contact us today.