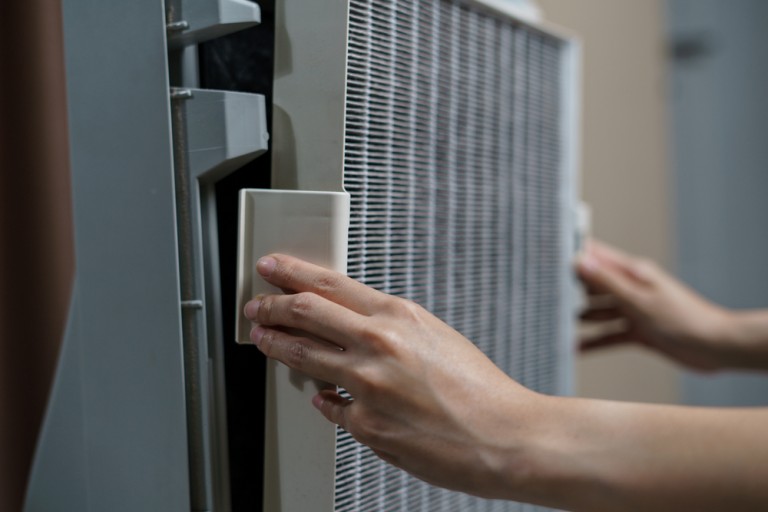
High efficiency particulate air (HEPA) filters are an integral component of laboratory and cleanroom safety and integrity infrastructure. HEPA filter pressure measurements are one of the key factors in proper HEPA filter testing and maintenance, and differential pressure is one of the most important metrics to track.
Here, we will look at why gauging the differential pressure across HEPA filter performance is so important, and we will examine how to use these measurements in the most effective way.
Measuring Pressure
Measuring and documenting pressure levels is important for multiple reasons. An example of this importance is that when pressure level measurements are combined with airflow measurement data, it becomes possible to assess remaining filter life. There are two main reasons that HEPA filters are replaced. The first reason is that the filter is damaged beyond repair and the second reason is that the filter is loaded to a point that it can no longer deliver the required amount of particulate free air.
This article explains how to use differential pressure trend data to more effectively manage and maintain HEPA filters.
Determining HEPA Filter Performance Trends
HEPA filter performance should be measured and recorded at defined intervals in order to effectively determine performance trends and pressure changes. The specific measurement interval should be selected based on a risk assessment that takes into consideration items such as previous trending data, the financial cost of product loss, and even replacement procurement time.
Trending the measurements is also a reliable way to identify scenarios that may require further investigation or corrective actions. Some examples of issues or items that could be detected from the data trending are, loaded filters, filter gasket issues, fan/blower issues including slipping drive belts, ductwork integrity issues, and airflow dampers that have unintentionally changed.
As HEPA filters are used, they filter out a minimum of 99.97% of all particulate matter present in the air, but that comes with a cost. The cost is that the filter will eventually become so loaded with that particulate matter that it can longer provide the required amount of particle free air. At this point the filter will need to be replaced. There are various factors that contribute to the life of a filter, but two main factors are the volume of air that passes through the filter and the amount of particulate matter present in that air. For example, filters used in high airflow applications or air with high particulate levels will require replacement sooner than filters used in lower airflow applications or air that is pre-filtered. While most HEPA filter manufacturers recommend a 3-5 year filter replacement, filters with excellent pre-filtration can last 10 years or more while filters subjected to high airflow and/or high particulate laden air may not even last 1 year.
Pressure trend tracking can also help detect catastrophic filter failure. For instance, if the pressure differential suddenly becomes far lower than a previous measurement, it could possibly mean the filter media has separated from the housing, the flex duct has blown off the filter housing, or that the blower/motor has a slipping drive belt.
Technical Safety Services is a lab and cleanroom testing and certification leader, performing extensive services for controlled environments, including environmental monitoring measurement and trends. To learn more about our services and how we can help improve the efficiency and effectiveness of your processes, contact us today.