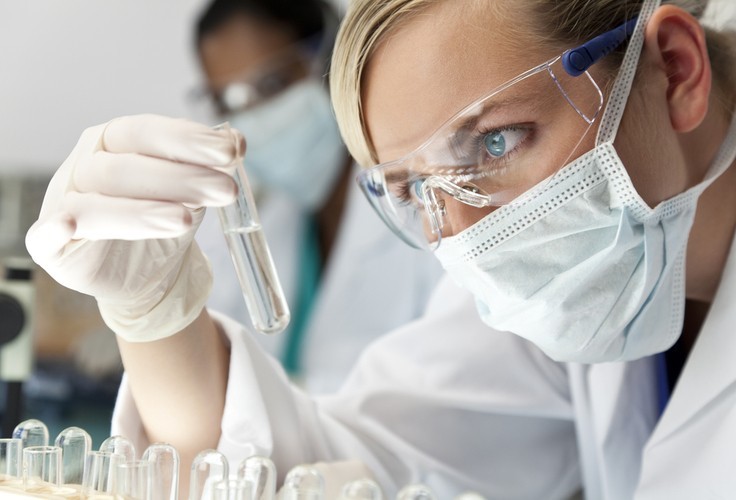
Professionals in industries such as medical device manufacturing, biotechnology, healthcare, pharmaceuticals, nanotechnology and more are conducting some of the most vital work in testing labs. Industrial lab safety, therefore, is critical to safeguard the health and well-being of these technicians, as is the protection of equipment, products, samples, supplies and the facility itself. The importance of testing lab safety cannot be overstated; it helps keep all of these components — most notably, workers — out of danger.
Lab Safety Risk Factors
The importance of testing lab safety is due largely to the number of risk factors present in a lab. These hazards include:
- Biological materials: Working with biological specimens such as germs, viruses and patient or donor samples can introduce several dangers. The most direct is that the person conducting these tests may be infected by the material in question. Other risks include contamination of air and surfaces that may spread to other employees.
- Chemicals: Chemicals present a major threat in testing labs. Whether through inhalation of vapors or contact with skin or eyes, these substances may cause harm to personnel in various ways, including burns, respiratory injury and neurological impairment. In addition, some chemicals can damage lab equipment.
- Glassware: In testing labs, glass is often the material of choice for handling samples and other materials due to its strength and inert properties. Glassware, however, also poses a number of hazards. Broken, chipped or cracked apparatuses may snag or tear PPE (personal protective equipment), compromising its integrity. Glassware should be carefully inspected prior to use to ensure that these risks are not present.
- Contamination or damage to samples or products: It also bears mentioning that any of the above risk factors can lead to adverse secondary effects. This includes contamination of tests, experiments or products intended for patient or consumer use. Once corrupted, results are useless, which could pose a threat to the integrity and reputation of a facility.
Testing Lab Safety Guidelines
Now knowing the dangers of lab testing, we’ll review some best practices and methods to promote safety at a testing facility.
- Conduct risk assessments: Every lab is unique, and while the above factors are likely to be present at nearly all facilities, some hazards may be more pertinent than others. Risk assessments examine each process in the testing lab, allowing personnel to zero in on the actual dangers existing in their specific workplace.
- Develop safety SOPs (standard operating procedures) and checklists: Once a risk assessment is complete, you are well-equipped to create a focused safety plan, including step-by-step procedures and requirements to follow.
- Ensure that all required safety equipment is readily available: PPE should be in stock and easily accessible by staff members at all times.
- Testing of all lab equipment: In spite of the risks, lab safety practices are extremely comprehensive and effective today. This is because of the development of proper procedures and the improvement of safety equipment, such as biological safety cabinets. Regular evaluation and maintenance are critical to ensure that personnel can use these tools as intended, with the confidence that they will be protected.
- Certification: Function certifications entail comprehensive testing and review of your equipment and procedures. This can provide you and your employees with the peace of mind that they will remain out of harm’s way as they work.
With expertise in facility commissioning, testing and certification, Technical Safety Services is ready to assist you. Our mission is to minimize the risks for your employees, equipment and testing lab. To learn more about our technical safety services, click here. To discuss your safety needs in detail, contact us today.