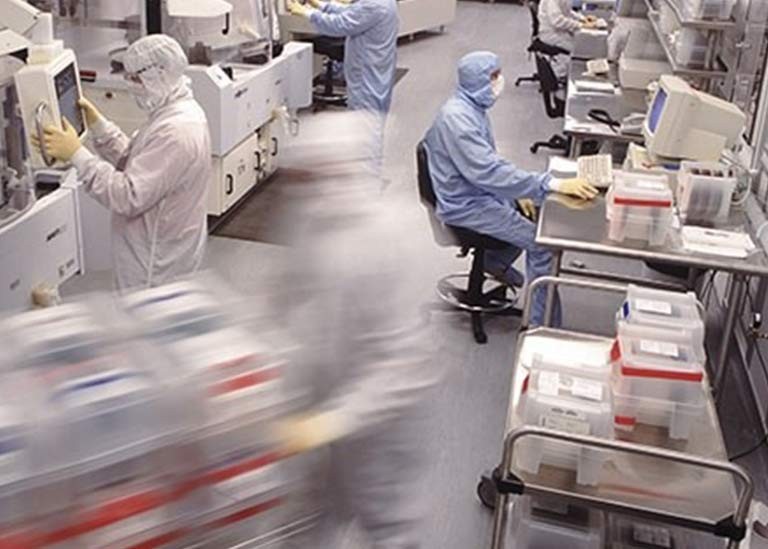
In cleanroom environments, control is critical, and air pressure is one of most important measures that must be closely monitored. Air pressure cascades are a highly effective way of controlling the flow of contaminants, ensuring that the cleanroom meets its performance objectives.
Cleanroom pressure cascade configurations employ pressure differentials to keep contamination moving from the areas that are intended to be kept the cleanest or most contaminant-free to areas with a higher contaminant threshold. In other words, a pressure cascade in cleanroom applications is used to move contaminants from the most critical areas to areas where higher levels of contaminants are acceptable. There are also many situations where pressure cascade is intended for high contamination containment to stop the migration of potentially disastrous contagions, chemicals, or gasses to the general public.
Why Is Cascade Design Important for Cleanrooms?
Pressure cascade design for cleanrooms is important because it helps to keep targeted areas and products, processes or people within acceptable levels of contaminants. While industrial processes in general should always focus on protecting people and products, cleanroom applications in particular necessitate a higher degree of control and contaminant management, which is why pressure cascades are useful.
Pressure cascades can serve a range of purposes. In some cleanroom applications, for instance, the primary concern is keeping products and processes below a certain level of contaminant presence. In these applications, the pressure cascade will be designed to move particles from the handling area to a less critical area, where contaminants can be further dispersed and safely expelled.
In other cases, pressure cascades are intended to keep contaminants from escaping the cleanroom. Such applications might include biomedical testing and sample handling. In these situations, the pressure cascade is configured to keep particles within the cleanroom or lab and it’s filtration system so that potentially hazardous materials do not escape and expose other personnel.
Without proper air pressure management, personnel – within or outside of the cleanroom – may be exposed to potentially hazardous materials, products (including medical or food products) may be contaminated, and the integrity of testing, handling and production processes may be threatened.
How to Design Pressure Cascades
Pressure cascades are primarily based on the principle of pressure differentials. Under this principle, air and the particulate matter that it holds flows from areas of higher pressure and resistance to areas of lower pressure and resistance.
An alternate way of looking at this concept is to consider air “supply” – areas of higher supply will flow to those of lower supply. Air “return” can also be controlled to manage a pressure cascade.
Pressure cascades must be carefully planned and implemented, taking into account door opening size, the seal of the room, availability of airflow and air movement capabilities (through ductwork and fans). In general, pressure cascades are created using a combination of ducting, dampeners and fans. A general rule of thumb is to have 0.020 inches water column differential pressure between ISO classified rooms and 0.050 inches w.c. between ISO classified rooms and non-classified rooms. Doors where differential pressure is critical normally do not have gaskets or sweeps to offset the supply vs exhaust values to ensure a higher rate of unidirectional air flow when the door is opened, and to limit damage to surfaces the gaskets or sweeps contact during door movement.
Technical Safety Services is a testing and certification leader, performing a broad range of services for controlled environments, including laboratories, cleanrooms, and research facilities. We are experienced in testing and validation for facilities, including air balancing and airflow adjustment for pressure cascades. To learn more, visit our testing page or contact us today.