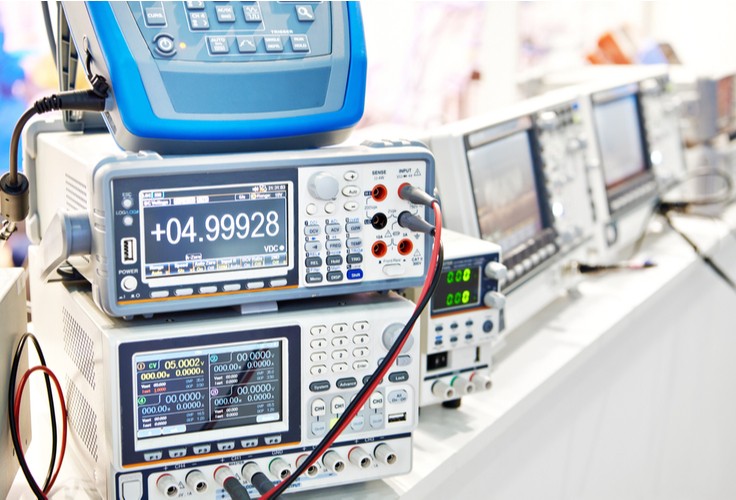
The reality of using any type of equipment is that over time it will drift out of calibration. This is an understood and generally accepted part of owning and operating laboratory and other technology. As such, methods of recalibration are typically straightforward and built into standard maintenance cycles — perhaps once a year.
Test equipment, however, is different. It is the machinery used in the calibration process itself: calipers, gauges, and so on. These apparatuses must be accurate, as their precision is among the most critical functions throughout the entire facility. The importance of calibration of laboratory equipment cannot be overstated. If test equipment is faulty, then anything it evaluates is also at risk of error, malfunction and even failure, which can affect the quality and integrity of your output and the safety of your operators.
So, how often should test equipment be calibrated? Due to the differences in equipment, environment, application, operator and other variables, there is no single correct answer. However, there are ways to determine the right calibration timeline for your specific situation.
How and When to Calibrate Test Equipment
Calibration is most often done by analyzing a process against a known, verifiable and traceable standard, which can be supplied by the manufacturer or other regulatory body. Due to the importance of test equipment, the calibration frequency of measuring instruments should generally be higher than that of other instruments. By evaluating and calibrating your measuring gear more often, you can have greater confidence in their performance.
Factors to consider when determining calibration recurrence include:
- Manufacturer recommendations: OEM specs are the best starting point. The manufacturer has the greatest amount of data about the machinery and can generate an accurate metric for when calibration will be required. However, keep in mind that although this number is a good starting point, it’s based on a sample size of the equipment and the average results, and thus will not be perfect.
- Tracking and data: As you carry out testing and recalibration, be sure to track measurements over time. You may find that the instrument remains in an acceptable calibration for longer or shorter than indicated by the manufacturer. Repeat the same procedure through several maintenance cycles to make a more accurate determination for your specific unit.
- Context: What are you using the equipment to measure? If it’s evaluating a critical process or component in your operations, you may want to calibrate your testing devices before every use, if feasible.
You should also consider creating a “must-calibrate” event list — aside from regular use, there are certain scenarios after which equipment should always be recalibrated. These include:
- Dropping an instrument
- Any impact or damage
- Equipment relocation
- Any incident where inaccurate calibration may have been a root cause
Calibration Services from TSS
Technical Safety Services provides proven lab equipment calibration with over 50 years of success and reliability. We are ready to calibrate your instruments and help determine the maintenance plan that’s right for you. To learn more about our capabilities, contact us today.