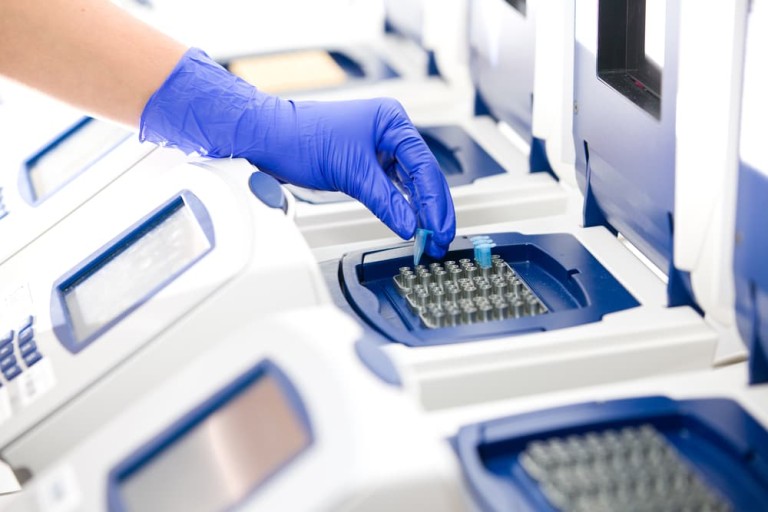
It is critical for equipment in laboratory settings to be properly calibrated in order to return reliable, repeatable results. Calibration helps to maintain accurate measurements, improve safety, extend equipment life, reduce maintenance, and maintain compliance and certifications.
It is especially important to follow rigorous calibration processes for temperature-controlled equipment such as incubators, freezers and refrigerators, as well as other lab equipment like pipettes and centrifuges. In laboratory settings, this type of equipment is typically used to maintain the proper controlled environment for microorganism cultures and samples being used for testing, research and medical product development.
Without proper calibration, not only is the viability of these samples threatened, but they may be compromised, altered or damaged, which can lead to compromised results and wasted time and money. Here, we will explore one of the most effective ways to achieve reliable, accurate calibration: through maintaining effective calibration criteria.
Explaining Calibration Criteria
Lab equipment calibration is often determined or guided by regulatory bodies such as the CDC, USP, FDA and others, including industry-specific regulators. Many laboratories and research facilities also establish their own sets of in-house guidelines, for numerous reasons: the materials at hand may require different a calibration tolerance, for example, or testing plans may require scenarios not described in manufacturer or regulatory guidelines. In the scenarios described in the introduction to this article, labs may also require a more stringent incubator calibration tolerance for sensitive microbiological material, for example.
When labs are setting their own calibration criteria, planning and documentation are more critical, given that such documentation cannot be found elsewhere since it is unique to the facility and the application. In the example of incubator calibration criteria, documentation should include, at a minimum, the parameters to be measured — temperature, humidity, CO2 and more — and the acceptable ranges within which they should fall. In the next section, we will explore calibration criteria in greater depth.
Establishing Calibration Criteria
When a facility is defining calibration criteria, it should consider:
• Sample requirement for stability/viability and storage guidelines
• Measurements to be tested
• The tool or instrument used for measurement
• The standard and traceability of the measurement tool
• The frequency or interval of testing
• Result documentation procedures
• Remediation and corrective action measures
• Calibration process and documentation
Calibration criteria should also consider accuracy, error, tolerance and uncertainty. These terms are used in similar scenarios, but have distinct meanings:
• Accuracy: Refers to the level of agreement between a measured value and an accepted reference standard
• Error: Refers to the difference between a measured value and an accepted reference standard
• Tolerance: The difference between the minimum and maximum acceptable measurements for a given parameter
• Uncertainty: Refers to the quantified dispersion or difference of measured values
Working With Technical Safety Services
Technical Safety Services offers a variety of calibration services, with the knowledge and expertise to help you calibrate to established standards, or to develop calibration criteria and a plan to meet your own in-house requirements. We specialize in calibration of temperature-controlled and thermodynamic equipment, including incubators, refrigerators, freezers, autoclaves, thermometers, ovens, water baths and more. To learn more, contact us today.