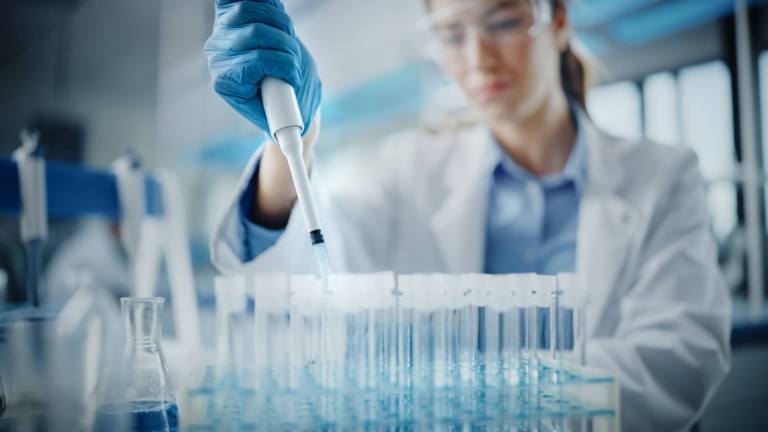
How clean is the air inside your cleanroom? By following industry best practices and adhering to ISO cleanroom standards, you have a better chance of avoiding the disruption and delays that come from having to shut down operations and bring your cleanroom into compliance.
Cleanrooms play a crucial role in various industries, from pharmaceuticals to semiconductor manufacturing. To ensure the highest levels of product quality and safety, these environments must adhere to stringent cleanliness standards.
The International Organization for Standardization (ISO) defines cleanliness standards for cleanrooms and associated controlled environments to provide objective information for facility owners and operators. Foreign particles, including microbes and dust, may degrade the integrity and the quality of your research efforts, cleanroom processes, and the products that you design, create, and sell.
ISO 14644-1 Cleanrooms and Associated Controlled Environments Part 1 defines cleanliness according to levels from ISO Class 1 to ISO Class 9, in order of most stringent to least stringent requirements. These requirements are based on the concentration of particles of a particular size in a volume of air.
About the Requirements for ISO Classes 1-9
Below is an overview of the ISO cleanroom cleanliness standards to give you greater insight into maintaining the appropriate level of cleanliness in your facility. If any questions arise about how ISO cleanroom cleanliness standards apply to your organization, please contact us today.
ISO Class 1
ISO Class 1 represents the highest cleanliness standard, often used for highly specialized tasks such as electronics that require nanotechnology or in the aerospace industry. It demands the lowest levels of particulate contamination allowing no more than 10 particles at 0.1 micron size or greater per cubic meter of air.
ISO Class 2
ISO Class 2 is slightly less stringent than ISO 1 but still demands very high levels of cleanliness. This level is common in industries like high-precision optics and high-tech electronics. It requires particle concentrations of no more than 100 particles at 0.1 micron size or greater and no more than 10 particles at 0.3 micron size or greater per cubic meter of air.
ISO Class 3
ISO Class 3 is suitable for applications where very clean conditions are necessary but not as extreme as ISO 1 and 2. This level is often used in medical device manufacturing and certain biotech processes. It requires particle concentrations of no more than 102 particles at 0.3 micron size or greater and no more than 35 particles at 0.5 micron size or greater per cubic meter of air.
ISO Class 4
ISO Class 4 standards are applicable to environments requiring a high degree of cleanliness but with less stringent requirements compared to ISO 1 through 3. This level is commonly used in research and development settings for electronics assembly, pharmaceutical production, and biotechnology. It requires particle concentrations of no more than 1,020 particles at 0.3 micron size or greater and no more than 352 particles at 0.5 micron size or greater per cubic meter of air.
ISO Class 5
ISO Class 5 environments are used in applications where clean conditions are required but are less critical than ISO 1 through 4. ISO Class 5 is often used in aseptic areas of pharmaceutical production and compounding, medical device manufacturing, and biotechnology research. It requires particle concentrations of no more than 3,520 particles at 0.5 micron size or greater and no more than 832 particles at 1.0 micron size or greater per cubic meter of air.
ISO Class 6
ISO Class 6 is less stringent and is used in environments where moderate cleanliness is sufficient. It is suitable for settings where product sensitivity is lower, such as certain types of manufacturing facilities. It requires particle concentrations of no more than 35,200 particles at 0.5 micron size or greater and no more than 293 particles at 5.0 micron size or greater per cubic meter of air.
ISO Class 7
ISO Class 7 represents a basic level of cleanliness suitable for environments where cleanliness is necessary but not as critical. This level is often seen in less sensitive manufacturing environments and to serve as preparation rooms for critical processes performed in ISO Class 5 or cleaner environments. It requires particle concentrations of no more than 352,000 particles at 0.5 micron size or greater and no more than 2,930 particles at 5.0 micron size or greater per cubic meter of air.
ISO Class 8
ISO Class 8 is typically the lowest level of cleanliness used for cleanroom environments and is suitable for areas where contamination risks are lower. It is commonly used in areas such as storage rooms, lower-risk manufacturing zones, and gowning areas prior to entering cleaner ISO Class spaces. It requires particle concentrations of no more than 3,520,000 particles at 0.5 micron size or greater and no more than 29,300 particles at 5.0 micron size or greater per cubic meter of air.
ISO Class 9
ISO Class 9 is generally not used for controlled environments and is commonly referred to as “room air”. This ISO Class often applies to standard office or industrial settings. It requires particle concentrations of no more than 35,200,000 particles at 0.5 micron size or greater and no more than 293,000 particles at 5.0 micron size or greater per cubic meter of air.
Each ISO Class will require varying levels of engineering controls, personnel/material transfer procedures and cleaning protocols to achieve and maintain the level of cleanliness required for each application.
A few considerations when developing and maintaining a cleanroom environment include:
- Use of HEPA/ULPA Filtration
- Room air exchange rates
- Room differential pressures
- Unidirectional and/or non-unidirectional airflow designs
- Materials used in the construction of the space
- Personnel gowning protocols
- Personnel ingress/egress procedures
- Material ingress/egress procedures
- Cleaning protocols
The above list is not exhaustive, but includes a few key considerations when designing and maintaining a cleanroom environment. These environments are often complex and require routine maintenance and monitoring to ensure they are performing as required for product quality and safety.
Technical Safety Services Offers a Wide Range of Cleanroom Testing Services
Technical Safety Services is the preferred provider of services to help organizations with testing and certification to ensure that their cleanroom facilities achieve and maintain compliance with ISO cleanliness standards. We have extensive experience with industries ranging from food and beverage, pharmaceuticals, biotechnology, hospitals, and other healthcare facilities, to medical device manufacturing, aerospace, and more.
To take advantage of our cleanroom testing services, please contact us today.