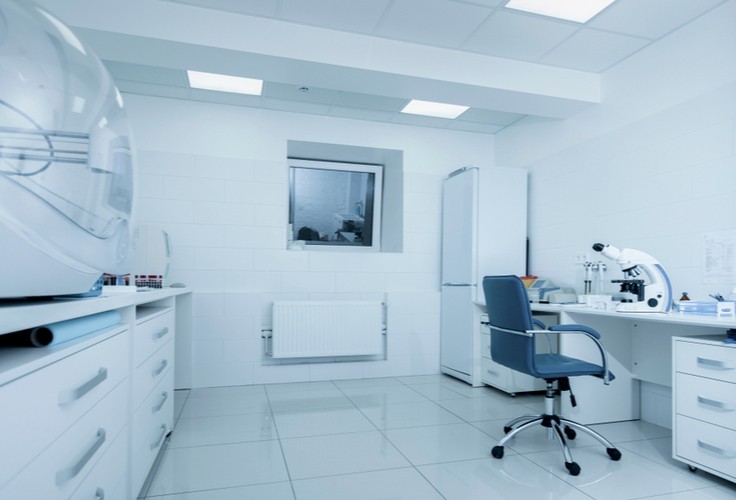
Many professionals involved in the research and development of cutting-edge technologies are familiar with the importance of cleanrooms. Whether you use yours for R&D, manufacturing or some other purpose, you are probably aware that these specialized controlled-environment spaces are designed to minimize, or effectively eliminate, the risk of contamination from all manner of airborne particulates.
While it’s virtually impossible to eliminate all conceivable contaminants — such as dust, airborne microbes, aerosol particles and chemical vapors — especially when humans are involved, cleanrooms are designed to reduce these potential problem-causing pollutants to an acceptable minimal quantity. This is typically expressed as the number of particles of a specified size (0.5 micron or larger, for example) per cubic meter of room air.
The Pursuit of Perfection
Ambient air contains an astoundingly high number of these particles. Ordinary room air, for instance, may contain about 1 million particles per cubic meter. City air may contain tens of millions of particles. Since no cleanroom can ever maintain a perfect zero, any cleanroom is classified by the quantity of particles per cubic meter based on the size of the particle (example, ISO 5 cleanrooms can have up to 3,520 particles that are 0.5 micron, or up to 100,000 0.1 micron particles, and only 832 1.0 micron particles).
Thus, industries and processes such as semiconductor manufacturing, pharmaceuticals, biotech, medical devices, life sciences, aerospace and optics depend on cleanrooms to reduce these particulates to acceptably low quantities. Some cleanrooms provide strict control over temperature, humidity, vibration, sound, VOCs, and light too.
Air entering a cleanroom passes through High-Efficiency Particulate Air (HEPA) filters. These remove the vast majority of micro particulates (99.97% of 0.3 or 0.02 micron particles). In some cases, cleanrooms may feature Ultra Low Particulate Air (ULPA) filters to achieve an even greater level of cleanliness (99.999% efficient at the same size). Some HEPA or ULPA filters are tested at smaller particles, and this is based on the Most Penetrating Particle Size (MPPS). When a filter is rated at 0.3 micron, it does not mean anything smaller passes through, actually smaller particles are trapped better due to Brownian motion. Particles that are not simple molecules (gasses) will be trapped in either filter.
Purpose-Driven Design
Not all cleanroom design standards are the same. The level or type of cleanliness may vary by many orders of magnitude, depending on the precise needs of your given process or task. Size varies, too, based on anticipated needs. Given that high-volume air handling and filtration is an energy-intensive endeavor, some users opt for the smallest spaces possible, to minimize expenditures.
When it comes to cleanroom construction requirements for your specified purpose, therefore, it’s important to know precisely how you intend to use it, and what level of filtration will be acceptable. Different industries and processes require different specifications. Whether or not hazardous materials will be used is another factor that affects design.
If you need to understand how to create a cleanroom, consider consulting the international publication: ISO 14644 Part 4: Design, construction and start-up, which explains the issues involved in planning and implementation. Furthermore, if you are involved in pharmaceuticals manufacturing or R&D, you will also need to reference the federal guideline on “Sterile Drug Products Produced by Aseptic Processing,” which details some of the requirements for this specialized industry.
Factors to Consider
Cleanroom design is far from simple. Before beginning your cleanroom, you should be able to answer at least five key questions:
- Which regulations will govern your design, based on anticipated use? Requirements vary widely, depending on your industry and proposed use. ISO class standards will vary, and process specific regulations will dictate certain parameters.
- What operating conditions will you require? Personnel will need to be able to work comfortably. Any particles, microbes, heat or humidity generated by them or ongoing processes must be accounted for. These variables can be calculated beforehand, based on equipment specifications and the number of workers who will occupy the space during a given shift.
- Have you envisioned the rough layout of the room — including its exits and entrances, and whether any key duties will be performed within, or without, the room? Again, HVAC considerations are crucial to maintain optimal temperature and humidity at all times.
- Do you anticipate using a biohazard cabinet or fume hood within the cleanroom? Filtration that exhausts to the outside will unbalance room air pressure, and must be taken into consideration. Alternatively, exhaust air may be cycled through filters and returned to the cleanroom, if feasible, to maintain pressure without adding more filtered outside air.
- What are your space parameters? This includes considerations regarding how high the ceiling can be, type of existing flooring on which you will be building, and how much power is presently available for use.
Certification and Testing
Obviously, once your cleanroom is designed, installed and operational, you will need to invest in ongoing certification and testing to help ensure optimal functionality. At Technical Safety Services, we offer comprehensive cleanroom certification services, including documentation created with eData — our proprietary, 21 CFR Part 11-compliant data collection software.
Cleanroom testing is performed by our trained, highly qualified technicians in accordance with current good manufacturing practices, Institute of Environmental Sciences and Technology, International Organization for Standardization, and any applicable customer design specifications. Primary testing includes six key tests, such as airflow volume/velocity readings, room air exchange rate, HEPA filter testing and more.
With every service call, Technical Safety Services offers you:
- Responsive service to minimize downtime
- Customized documentation and technical writing services
- Online access to your equipment inventory and certification
- The assurance of ISO 9001-certified quality
For more information about our comprehensive suite of cleanroom testing options, contact us here.