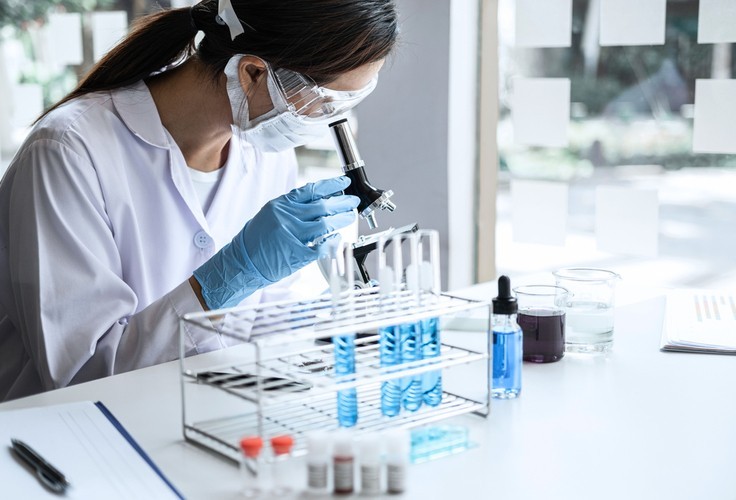
Introduction to Validation Master Plans
In pharmaceutical manufacturing facilities, a validation master plan or VMP is a document companies use to ensure that they consistently create products that adhere to standards of quality and government regulations. Master plans are critical because they give companies a systematic approach to validating the systems, processes and equipment they rely on during production.
A validation master plan fits into your overall validation strategy by helping optimize what occurs at control points where variations in production might occur, which is part of the strategy to keep products safe and effective as they move through the production process.
Integrating the validation master plan with your broader validation and compliance framework is instrumental in reducing risks and avoiding product recalls or failures.
For example, you use the VMP to meet requirements of the Food and Drug Administration’s Quality System Regulation (QSR). If you manufacture products for distribution in the European Union, your VMP will address regulatory expectations of Annex 15 of the EudraLex Volume 4, which has to do with validating computer systems, equipment, processes and cleaning.
You can expect that regulatory inspectors will want to review your validation documents to gain an overview of how your organization addresses validation tasks, what specific risks are involved in producing products and what steps you’ve identified to address these risks.
Keep in mind that the VMP is not a static document. Companies must occasionally review their validation master plan to ensure it meets current industry best practices and regulations. Validation activity must keep up with changing conditions.
The validation master plan shows your team and regulators what elements must be validated in your facility as you follow standard operating procedures to meet quality assurance requirements.
Accordingly, the VMP is a vital document that you can use to manage and educate current employees as well as when onboarding new staff.
Key Components of a Validation Master Plan
Essential elements of a validation master plan include:
- Describe the scope of the project.
- Identify the objectives of the validation master plan.
- Refer to the guidelines and standards your team should work toward.
- Provide details on the schedule for validation activities.
- Note your validation policy and the approach you take to validation to meet quality and regulatory demands.
- Explain the key personnel and their validation responsibilities.
- Define your strategy for validating equipment, processes and systems.
- List the documentation standards you employ for validation tasks.
- Show how your facility reviews processes and specify the steps it takes to analyze and continuously improve processes, especially in light of any new regulatory requirements that would impact your validation policy.
Validation protocols and checklists integrate into the master plan by providing a clear roadmap about what your team needs to do and according to what schedule.
Risk assessment is a central theme of your validation protocol, as it’s of paramount importance to keep people safe when using your pharmaceutical products. Incorporating risk management and risk assessment tools is prudent to help your stakeholders identify and mitigate potential validation issues.
You might prefer to partner with third-party experts to shore up your VMP or verify you’ve successfully updated the validation strategy as regulations or best practices evolve.
Developing a Validation Master Plan
Here is a step-by-step guide on drafting, reviewing and approving a validation master plan:
- Define your company’s policy toward validation in support of ensuring quality control and regulatory compliance, which are essential for maintaining consistent product quality.
- Define the areas of responsibility for management, the validation team and other personnel who support validation processes.
- Spell out the organizational structure of your validation team.
- Obtain buy-in and approval from key workers involved in validation, quality assurance and quality control, and all manufacturing and engineering processes. This includes subject matter experts in product development, packaging and maintenance engineering.
- Determine and then list the systems, processes, equipment and facilities you must validate, by listing laboratories, manufacturing areas and raw materials storage. Include reference images.
- Provide a list of abbreviations and a glossary to keep your documentation’s terminology consistent and to clarify ideas for regulators and employees consulting the master plan.
- Spell out the “key acceptance criteria” for measuring whether you’ve successfully completed a validation activity.
- Note the documents you refer to that support all validation tasks, such as process validation protocols and cleaning protocols. You’ll list information about installation qualification (IQ), operational qualification (OQ) and performance qualification (PQ).
- Highlight details of your facilities’ HVAC system (such as environmental conditions monitoring and your level of air filtration), and your water systems with descriptions of what measures you’ve taken to filter water and ensure its purity for pharmaceutical production.
- Include a section showing supporting documents, such as ongoing facility development reports, and your list of standard operating procedures on processes, equipment and systems. This is also where you’ll list manufacturer’s recommendations and instructions as well as details about the specifications of raw materials and the finished products and how they affect your validation approach.
- Explain your organization’s approval process, such as which key personnel are responsible for signing any validation documents, to show you are complying with government regulations or internal company standards. This will naturally include quality control sign-off.
- Security reports are crucial too, necessitating that you document your access control, such as with security guards and key cards, and by installing surveillance cameras.
- Show how you obtain and record testing data to verify that your manufacturing and cleaning processes meet government standards.
How can teams ensure the validation master plan remains relevant and up to date? They should conduct regular reviews of your systems, processes and equipment. This is a particularly important task when you plan to upgrade or swap out equipment or change a manufacturing process.
Common pitfalls in developing a validation master plan and tips for avoiding them include:
Poor documentation: Take time to ensure you’ve outlined all the reports, protocols and other documentation from various sources (internal as well as from equipment manufacturers) to support your validation project.
Unclear view of the scope of the validation processes: Undertake a comprehensive risk assessment to ensure you’ve opened the scope of what tasks go into your validation master plan.
Regulatory Changes: Designate one or members of your validation team to stay on top of any current or upcoming changes to government regulations to ensure you stay compliant.
Insufficient Training: Review your onboarding protocols to verify new recruits understand the role they play in the validation process.
Miscommunication: Keep communication channels open between all validation managers, quality assurance teams and other stakeholders. You will want to schedule regular meetings with team leaders to boost engagement and avoid making mistakes during validation processes.
Data integrity: Software validation is crucial. Ensure you keep your computer systems updated (OS and applications) and that you have robust security in place to help ensure the quality of the data you collect and report on during validation processes. Leverage technology to analyze this information and produce reports. Of course, data integrity will depend on regularly calibrating test equipment, which includes using modern validation temperature-controlled units.
Mismanagement of change control: Your validation efforts will go for naught if you do not manage changes to systems, processes or equipment. Consult with experts if you find it challenging to establish a strong change control protocol.
Lack of resources: Pharmaceutical companies must ensure they have enough resources in terms of equipment tools, spare parts, employees and time to properly schedule the tasks and activities described in the validation master plan. Otherwise, you risk falling out of compliance with regulations or failing quality assurance tests.
Being aware of these common challenges in validation planning and addressing them immediately will help ensure that you’ve developed a robust and effective master plan, which makes for a much smoother validation process.
The Role of a Validation Master Plan in Regulatory Compliance
The validation master plan is critical in supporting your organization’s regulatory compliance and avoiding penalties. It documents your ongoing processes and shows how you’ve met the quality assurance and regulatory standards.
Non-compliance with validation processes leaves your company subject to intensive audits, product failures or even product recalls.
You would then face downtime, idling workers and machinery until regulators have assured themselves that you now adhere to the requirements of producing pharmaceutical products safely and consistently. What’s more, your organization could suffer a major hit to its reputation in the marketplace, damaging your financial standing.
Organizations can leverage their validation master plan during audits and inspections by providing clear, comprehensive documentation, checklists and historical data showing how they’ve created a proper process validation system with excellent quality assurance and quality control.
Showing how you handle deviation reporting and assessing any deviation’s impact and then what corrective measures you adopt will help give regulators more confidence in your validation processes to achieve compliance. The documentation will support your claims for rigorous operational qualification and performance qualification.
Connect With Technical Safety Services for cGMP Validation Services Today
As you can see, a validation master plan drives compliance and quality assurance by spelling out what activities your staff must do and the schedule for these tasks.
Your team’s validation effort plays a pivotal role in ensuring regulatory compliance and maintaining product quality, so you’ll avoid product failures and potential product recalls.
Organizations aiming to develop a robust validation master plan should get input from all validation activities stakeholders. This is critical for verifying you’ve addressed how your systems, equipment and processes adhere to quality standards and regulatory requirements. You’ll know that your systems and processes work according to design specification.
It shows you and regulators at a glance the validation activities used in your facility, ranked according to their relative priority for mitigating risk. You also refer to the VMP when scheduling validation processes.
The validation master plan is a living document that you’ll need to update whenever you change processes, install new equipment or when it’s time to adhere to updated government regulations. Your team must continuously evaluate and adapt the VMP to reflect such changes.
Companies that need assistance from third-party experts can rely on Technical Safety Services’ professional cGMP validation services. For more information about our validation plan services, please contact the experts at Technical Safety Services today.