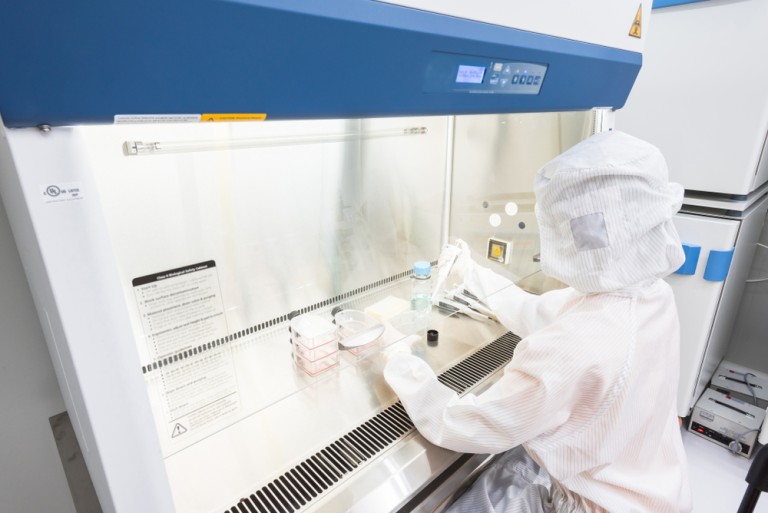
Introduction to Equipment Qualification in the Pharmaceutical Industry
Why is equipment qualification critical in the pharmaceutical industry? Your employees and customers depend on your pharmaceutical equipment working properly according to its design specification to meet quality control standards.
To verify that your pharmaceutical manufacturing facility adheres to Good Manufacturing Practice standards, rigorous, ongoing equipment qualification should be part of your standard operating procedures. Doing so supports product quality and helps ensure regulatory compliance. This is the case whether you produce a medical device or a medication.
Consider that professionals tasked with quality assurance in the pharmaceutical industry must regularly inspect, maintain and repair laboratory equipment, always verifying that devices are properly calibrated to deliver consistent results.
Regulatory requirements for equipment qualification are governed by a vast array of regulations, including from the Food and Drug Administration (FDA) and guidelines established by the Management Board of the European Medicines Agency (EMA), which you’ll want to pay close attention to if you plan on selling products to international customers.
You should know that equipment qualification impacts pharmaceutical product efficacy, quality and safety, and requires manufacturers to establish robust validation processes.
Key Steps in the Equipment Qualification Process
You may hear industry experts refer to equipment validation or equipment qualification interchangeably. We refer to qualification to address equipment such as instruments and pipework, and validation to address manufacturing processes, such as cleaning equipment, manufacturing items and running computer systems. A validation plan is essential for an organized equipment validation process. This includes establishing acceptance criteria, which must be met in order to consider your equipment is properly validated.
For an overview, here are critical steps in the equipment qualification process to be aware of. Begin with Requirement and Specification Generation, then address Design Qualification before you proceed to Installation Qualification and then Operational Qualification, which is followed by Performance Qualification.
Design Qualification (DQ)
After you’ve determined the requirements and specifications of your system, the equipment qualification process begins with design qualification (DQ). A validation engineer should double-check the equipment design will be safe and accurate, functioning according to government regulations.
Installation Qualification (IQ)
During installation qualification, verify that the equipment is installed in keeping with the manufacturer’s specifications and meets your organization’s usage and quality standards. An engineer needs to inspect plumbing, mechanical parts and wiring, seeing that they are installed properly.
Operational Qualification (OQ)
At this point, test the equipment to see whether it functions in line with your operational specifications (taking into account the manufacturer’s stated specifications) under normal operating conditions as well as what happens during worst-case situations. In OQ, an engineer tests the limits of the equipment to verify it will function under a range of operating conditions without compromising quality or outright failing.
Performance Qualification (PQ)
Finally, take care of performance qualification, testing that the equipment in your pharmaceutical facility works correctly under routine operating conditions, in a consistent manner that your team can depend on. You’ll test the system as if you were doing an actual production run, keeping watch over performance characteristics with the goal of signing off on its ability to deliver the high-quality results you expect, time and time again.
One common issue that companies face during instrument calibration is failing to adhere to the inspection and calibration schedule, which you will work out according to the manufacturer’s specifications.
If an instrument is giving inconsistent results, calibrate it immediately rather than waiting for the next scheduled calibration event. To address calibration issues, you should know what the objective readings should be and use them as benchmarks to verify you have correctly calibrated the equipment.
It’s helpful to consult the historical records on each piece of equipment, to see if there are any patterns indicating possible future failure. Spotting calibration drifts will help you formulate a proactive adjustment process.
With improperly calibrated equipment, you risk compromising product safety and efficacy and potential fines stemming from failing to adhere to regulations, with the threat of product recalls.
Standard Operating Procedures
Your organization must develop and implement effective Standard Operating Procedures (SOPs) for equipment qualification to verify compliance and efficiency during manufacturing. Creating SOPs requires knowing current industry best practices, backed up with experience and deep knowledge of equipment validation processes — which you can outsource if you lack this expertise in-house.
Best Practices for Instrument Calibration
Recognizing that calibration involves comparing objective benchmark measurements to the actual tool measurements, you will want to schedule inspections, maintenance and calibration on a regular basis. Depending on the nature of the equipment and the manufacturer’s guidelines, you may be calibrating tools once a month or once per year.
Following best practices, have a professional calibrate any equipment that is on schedule for the latest verification. Also, begin calibration on any equipment that has been bumped, dropped or disturbed in your manufacturing facility. If you see measurements that run outside of the anticipated range or if you hear strange sounds, you’ll want to initiate calibration immediately.
You can rely on the professionals at Technical Safety Services to take care of accurate instrument calibration on your behalf. Doing so helps reduce the total cost of ownership of your equipment, extending its lifecycle, as well as ensuring your ongoing regulatory compliance and certification.
Understanding the Difference Between Equipment and Process Validation
What distinguishes equipment qualification from process validation?
Equipment qualification has to do with inspecting and verifying that machinery and other equipment works correctly during the manufacturing process.
Process validation involves checking that your procedures work safely and are reliably consistent.
Both equipment and process validation are crucial for pharmaceutical manufacturing as they cover the way you manufacture products and the equipment that you use to achieve your production goals. Equipment and process validation are interdependent, hence the critical role of both validation types to ensure you adhere to regulations and meet your product quality benchmarks.
Pharmaceutical companies ensure that their equipment and process validation practices meet regulatory standards by devising clear strategies to align the equipment and process validation with current pharmaceutical standards and regulations. In many cases, manufacturers will outsource some of this work to third-party experts to ensure operations go smoothly and efficiently during validation.
Ensuring GMP Compliance During Equipment Qualification
Good Manufacturing Practices (GMP) compliance integrates into equipment qualification as the validation verifies that each piece of equipment in your manufacturing processes meets regulations for quality standards.
Common pitfalls in achieving GMP compliance include failing to train personnel on proper usage and maintenance, lack of qualified, competent personnel and poor documentation. Manufacturing facilities that do not keep up with sanitation and cleaning protocols may also experience challenges meeting GMP compliance.
Avoid such issues by creating and implementing rigorous standard operating procedures for staff to follow, onboarding workers with these SOPs in mind and underscoring the importance of maintaining detailed records on equipment performance and maintenance. Following a strict maintenance schedule is critical in achieving GMP compliance.
Essential documentation for proving GMP compliance in equipment qualification includes test reports, records of calibration efforts and audit trails. You also must record any deviations and what steps you took to correct the situation and bring equipment back into compliance.
Developing Effective SOPs for Equipment Qualification
Key elements of an effective SOP for equipment qualification include establishing specific operating procedures for each piece of equipment, based on manufacturer specifications and production histories for these devices that you maintain and keep track of in-house.
You also should include maintenance duties and calibration processes in your SOPs. When your tests and inspections indicate deviations from normal operating ranges, your SOPs should detail the procedures to document and handle these mismatches between what’s expected and what the tests indicate.
You want to develop good SOPs to prepare for and facilitate internal audits in preparation for regulatory audits and inspections.
Pharmaceutical Companies’ Success Depends on Mastering Equipment Qualification
Pharmaceutical manufacturers rely on equipment qualification to ensure they meet goals for product quality and remain in adherence to industry regulations. By establishing stringent standard operating procedures and keeping up with calibration requirements, you will be in a better position to pass inspections and regulatory audits.
The experts at Technical Safety Services have years of experience helping
pharmaceutical industry companies succeed with vital services such as ensuring operational qualification and equipment qualification. To learn more about our capabilities and how they can help you improve operations, please get in touch with us today.