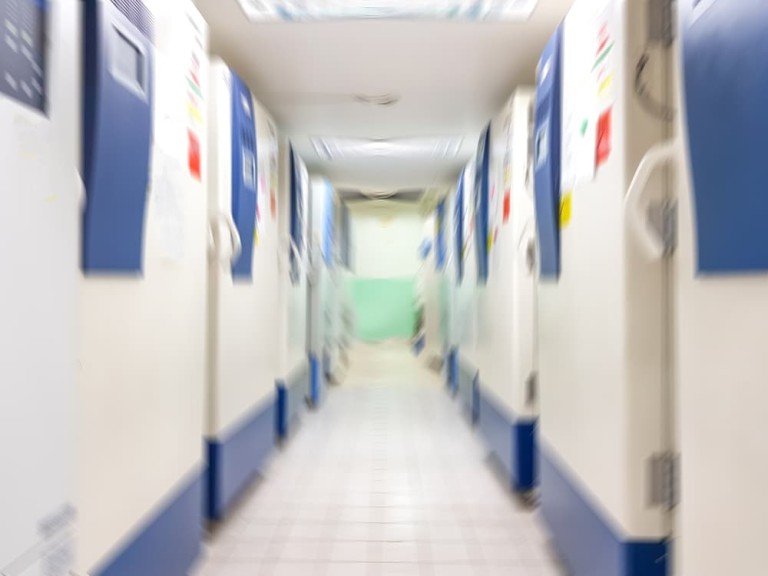
Freezer validation is an important process for pharmaceutical labs, medical manufacturing facilities and other life science and clinical markets where samples, drugs, raw materials and even vaccines must be stored at safe, usable temperatures. This requirement is not only to ensure the integrity of the product, and the efficiency of the equipment, but also to remain in compliance with FDA regulations and other regulatory bodies.
Here, we will examine some of the core tenets of freezer and other cold storage validation protocols, including freezer calibration and testing processes.
Calibration and Functional Testing
Prior to the temperature mapping portion of a full validation, the unit is thoroughly tested for all common functions and features to ensure proper operation. Then, a single point calibration is performed, confirming the display of the temperature inside the cabinet is within tolerance with a NIST-traceable temperature probe and device. Adjustments are made, if needed, to optimize the single point-in-time readings in preparation for temperature mapping. The mapping will then provide the supporting data that multiple points are within a defined tolerance over a specified period.
Temperature Mapping
Temperature mapping involves an empty cabinet run at the desired setpoint over a period with multiple monitoring probes located throughout the cold storage unit. This identifies that the unit is performing properly prior to a loaded study and is commonly part of the overall Operational Qualification (OQ). In a real-world scenario, however, a fully loaded freezer is likely to maintain a more stable temperature due to the mass (and thermal storage) of its contents. Many laboratory and industrial freezers are ultra-low-temperature (ULT) freezers, which operate differently than standard consumer freezers that use a fan to distribute cold air. ULT freezers use direct conduction from evaporator coils embedded in the walls of the freezer cabinet and the heat transfer from the cooled shelving inside the unit. Regardless of the heat transfer method, freezer, refrigerator, or even an entire cold room; temperature mapping gives you the initial data to qualify the unit for the next level before release for us.
Performance Qualification
Once the empty mapping has been completed, the performance qualification (PQ) reports those same probe locations over that same timeframe with the unit in a loaded or simulated loaded condition. This allows you real-time data on heat load, air flow, and possible loss of temperature that can occur in normal and “worse-case” operational scenarios. Some of those scenarios are also depicted in what is called the “excursion testing”.
Door Open and Power Fail Recovery
Door open recovery refers to the time that it takes for the cooling chamber to return to the required temperature after the door being opened, for example, to place or remove samples. Maintaining the consistent probe locations from the initial mapping and performance qualification mapping reports initial heat load effects, time to reach alarm conditions, and finally, the recovery time back to original setpoint once the door is closed. Similarly, monitoring the time frame for samples to maintain temperature within range after a power failure provides vital information for cold storage products. The time for the unit to recover is also reported as an additional excursion test. Unlike the door recovery excursions, occurring as more of a day-to-day function, power failures are a reality that have documented actions to mitigate the risks in loss of precious samples in a “worse-case” condition.
External Alarm Testing
If freezers fail, lose power, or stay open for too long, samples and products can be damaged or lost. Alarms must be in place to sound and work properly when failure or other scenarios occur, so that proper corrective action can be taken to secure or save the materials being stored. Alarm testing should accompany excursion testing to provide the information needed to determine alarm high and low setpoints and delays for notification and corrective action.
Validation and Re-Validation Services
Freezer testing and validation are critical components of a laboratory’s operations, ensuring that samples and other products are handled and stored properly. Validation and re-validation are critical for ensuring a traceable process for audits and other certification procedures. Proper execution of these protocols must be carried out by the right personnel to ensure the continued operation and success of the facility. Proper documentation, as-found and as-left readings, and equipment history must be available for inspections, audits, and testing.
Technical Safety Services provides comprehensive validation services for laboratories and pharmaceutical facilities, including freezer testing and validation. To learn more about how we can help you stay in compliance, contact us today.